Veronte Autopilot Integrates Advanced INS
Inertial Labs, Inc. and Embention Complete Full Integration of Inertial Navigation System (INS-P) and Veronte Autopilot.
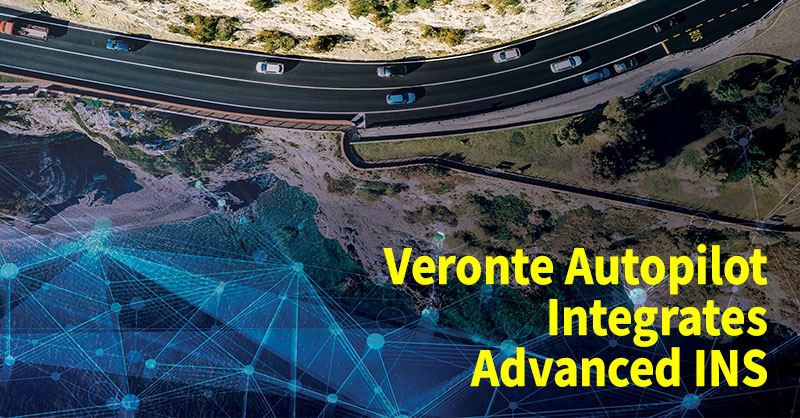
In November 2019, Inertial Labs announced the successful benchmark integration with Embention's Veronte Autopilot.
Embention began investigating Inertial Labs as a supplier for inertial measurement units (IMU) in 2013.
In subsequent years, the Inertial Labs Inertial Navigation System (INS) became an appealing GPS-Denied navigation source for Embention.
Veronte Autopilot Integrates Advanced INS
In 2016, Embention and Inertial Labs started discussing integrating the INS-P, the professional version of the INS, with the Veronte Autopilot.
After years of work, Inertial Labs announced the integration was complete and validated through testing.
The release is now available for purchase.
Customer Favorite
Initially, Inertial Labs released the INS product line in 2006.
Today, the INS line is in wide use in many applications.
Plus, it has proven its outstanding reliability and accuracy in challenging conditions -- high vibration, extreme temperatures, and tough mission profiles.
With integration complete, the INS is fully compatible and ready for autonomous unmanned flight system applications.
Tactical Grade IMU
The IMU component is tactical grade.
It is reliable for tactical guidance, navigation, flight control, stabilization, pointing systems, and other applications.
With Angular Rates and Accelerations data transfer rate reaching up to 2000 Hz rate, the low power consuming IMU provides an excellent SWAP-C advantage over legacy IMUs based off tactical grade fiber-optic gyros (FOG).
Plus, the on-board GNSS receiver is fully configurable to reach real-time position accuracy on one centimeter.
Veronte Autopilot
The Veronte Autopilot by by Embention features many top-of-the-line options which distinguish it in the marketplace.
Such features include: extended efforts for line of sight (LOS) and beyond line of sight (BLOS) communication, intuitive and high-performing software, and a configurable navigation solution for various applications - it is fast becoming a customer favorite.
Additionally, with the navigational accuracy provided by the INS-P, the autopilot offers highly accurate navigation in a GNSS-denied environment.
Plus, it is compatible with mission critical items such as tracker antennas, flight simulators and camera payloads.
This platform solution can customize to fit the needs of the end user.
About Inertial Labs, Inc.
Established in 2001, Inertial Labs is a leader in position and orientation technologies for both commercial/industrial and aerospace/defense applications.
About Embention
Founded in 2007, Embention develops components and critical systems for UAS.