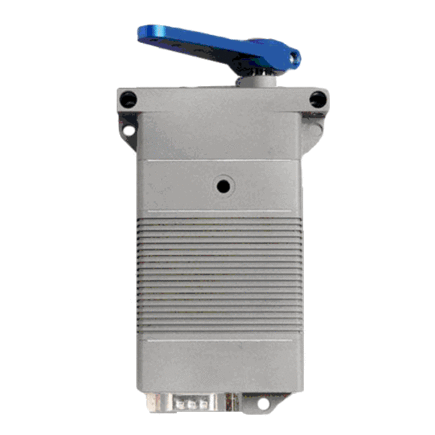
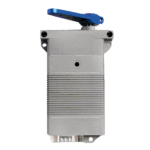
DA 26-30-5024 Volz Servo
DA 26-30-5024 Volz Servo guarantees maximum safety and reliability; features a brush less motor and a contactless wear free position sensor.
View cart
- Description
- Specifications
Description
DA 26-30-5024 Volz Servo guarantees maximum safety and reliability; features a brush less motor and a contactless wear free position sensor. This means maximum service life with the greatest-possible power delivery and its design prevents electromagnetic emissions (EMI) caused by brush sparking. The housing made of saltwater-resistant aluminum is HART-coat treated, meets the IP-67 standard for water and dust sealing and provides an integrated Sub-D connector (MIL spec. circular connector or cable gland on request). Brackets integrated in the housing for horizontal and vertical assembly. 6-fold, ball-bearing supported, steel gear train, drive shaft with ANSI multi-tooth (square shaped drive shaft on request).
The DA 26 series can be equipped with a standard PWM input (Pulse Width Modulation) that has two different interfaces: a differential, galvanic isolated interface (Opto-Coupler) and a single-ended interface with CMOS levels that is also used to program the servo parameters. IT includes analog position feedback to detect the drive shaft position. A differential RS-422 PWM interface can be chosen instead of the opto-coupled interface.
The DA 26 with digital serial command interface (RS-485) receives its commands via a CRC secured protocol. It can return not only shaft position in digital format, but also several diagnostic data such as the level of the supply voltage, current consumption and the temperature of the motor and electronics in digital form (optionally also humidity within actuator case). These kind of diagnostic capabilities help to determine the health state of the actuators before, during and after deployment.
DA 26 actuators have been subjected to endurance test of more than 3 million cycles (>2,000 hours). Furthermore, successful tests based on MIL-STD 810F (vibration) and 810G (acceleration/shock) have been performed. DA 26 actuators are used, for instance, in Schiebel Camcopter S100.
About Volz Servos
A servo from Volz excels due to the simplicity of its design while simultaneously maximizing positioning force, reliability and durability. Moreover, a variety of electric interfaces makes it possible, for instance, to monitor the operating condition of the servos by reading out the current consumption, the internal temperature and humidity, etc.
Every actuator compromises a DC motor, a gear train and control electronics governed by microprocessors with integrated position feedback. These are electromechanical servo units that precisely position a radial output drive.
Depending on the type of actuator, the maximum travel in the standard configuration varies between 90° and 170°. Versions with larger travel of up to 330° or “Multiturn” versions can be provided on request.
About Volz
Founded in 1983, Volz Servos began designing, manufacturing and marketing exclusively electro mechanical actuators/servos worldwide. Volz has developed a product range that meets most customer requirements concerning maximized torque, speed, efficiency, reliability, and durability at minimized volume/weight, component and development costs. Volz has a reputation for being experts in the market of compact, highly efficient actuators/servos.
Operating Data
Supply Voltage (rated) | 28 V DC |
Supply Voltage Range | 20…30 V DC |
Standby Current at rated voltage | Rated Current at rated voltage 0.8 A |
Peak Current at rated voltage | 1.3 A |
Rated Torque at rated voltage | 2.7 Nm (23.9 lbf-in) |
Peak Torque at rated voltage | 5.0 Nm (44.3 lbf-in) |
No Load Speed at rated voltage | 290°/s |
Rated Speed at rated torque | 200°/s |
Default Travel Angle | ±45° = 90° total travel |
Max. Standard Travel Angle | ±50° = 100° total travel |
Extended Travel Angle (optional) | ±85°=170° total travel |
Backlash (mechanical) | 0.5° |
Position Error under Temperature | ±1.0° |
Operating Temperature | -30°C … +70°C (-22°F…+158°F) |
Storage Temperature | -55°C…+85°C (-67°F…+185°F) |
Command Signal
Signal Voltage Levels | TTL-Level HIGH: min. 3.5V; max 5.5V |
TTL-Level LOW: min 0.0V; max 1.5V | |
Frame Rate | 2.6…2000 ms |
Valid Pulse Lengths | 0.9…2.1 ms |
Pulse Length for Position Left/Center/Right | 1.0/1.5/2.0 ms |
Resolution | ≤1.0us |
RS 485 COMMAND SIGNAL | Valid for all versions with RS 485 Command Signal |
RS 485 | RS 485 Redundant |
Baud-Rate | 115200±1.5% bits/s |
Protocol (documentation available) | 6 Byte (incl. 2 byte CRC) |
RS 485 Protocol Specifications
RS 485 | RS 485 Redundant |
Number of Data Bits | 8 |
Number of Stop Bits | 1 or 2 |
Parity | None |
Command / Response Frame
Byte # | Description |
1 | Command / Response-Code |
2 | Actuator ID |
3 | Argument 1 |
4 | Argument 2 |
5 | CRC High Byte |
6 | CRC Low Byte |
Material & Protective Features
Case Material | Saltwater resistant Aluminum Alloy |
Splash Water Resistance | IP 67 waterproof to 1m depth |
Case Surface Treatment | HART-Coat |
Salt Water Resistance | >100hrs. Salt Water Spray |
Standard – Case Material | |
EMI / RFI Shielding | Case Shielding |
Motor Type | Brushed DC Motor |
Gear Set Material | Hardened Steel |
Position Sensor | Contactless |
Position Feedback | Standard |
RS 485 Communication Interface | Optional |
Humidity Sensor | Optional |
Temperature Sensor | Standard – Motor and PCB |
Dimensions | DA 26-30-5024… |
Case Dimensions | 54 mm x 102.8 mm x 26.0 mm ±0.2 mm (2.123 in x 4.047 in x 1.024 in ±0.008in) |
Weight | 270g (9.50 oz) ±10% |
ELECTRICAL CONNECTION OPTIONS | DA 26.30.5024.1… |
Standard Connector | |
Manufacturer | ITT Cannon |
Type | DEMM-9PE |
Mating | D-SUB DE-9f |
PWM-OPTO Pin Assignment | ||
1 | PWM (AO) | Command Signal – Anode Optocoupler |
2 | PWM (CO) | Command Signal – Cathode Optocoupler |
3 | Diff FB A | Differential Position Feedback Signal |
Output A | ||
4 | to Pin 7 | Connect to pin 7 (ground) |
RS 485 Pin Assignment | ||
1 | +V DC | Supply Voltage |
2 | RS 485 A | Non Inverting RS 485 Input/Output (A) |
3 | GND | Supply Ground |
Interface Ground | ||
4 | RS 485 B | Inverting RS 485 Input/Output (B) |
Integrated MIL-Specified Electrical Connector
MIL-specified electrical Connector | ||
Manufacturer | Glenair Inc. | |
Type | #/Nr. 801-011-07MT6-4PA | |
Mating | #/Nr. 801-007-… | |
801-008-… | ||
PWM Pin Assignment | ||
1 | +V DC | Supply Voltage |
2 | Pos FB | Position Feedback Signal |
3 | GND | Supply Ground |
Signal Ground | ||
4 | SIG | Command Signal |
5 | Case GND | Case Ground |
6 | +V DC | Supply Voltage |
7 | GND | Supply Ground – Signal Ground |
8 | Pos FB | Single Ended Position Feedback Signal |
9 | Diff FB B | Differential Position Feedback Signal – Output B |
PWM-TTL Pin Assignment | ||
1 | NC | Do not connect |
2 | NC | Do not connect |
3 | Diff FB A | Differential Position Feedback Signal – Output |
4 | PWM | Command Signal |
5 | Case GND | Case Ground |
6 | +V DC | Supply Voltage |
7 | GND | Supply Ground |
Interface Ground | ||
8 | Pos FB | Single Ended Position Feedback Signal |
9 | Diff FB B | Differential Position Feedback Signal – Output B |
Rs 485 Interface (2-Wire) DA 26.30.5024.3…
RS 485 (2-Wire) Pin Assignment | ||
1 | RS 485 A | Non-Inverted Input/Output |
2 | RS 485 B | Inverted Input/Output |
3 | – | Do not connect |
4 | +V DC (2) | Supply Voltage – Secondary |
5 | Case GND | Case Ground |
6 | +V DC (1) | Supply Voltage – Primary |
7 | GND (1) | Supply Ground – Signal Ground – Primary |
8 | GND (2) | Supply Ground – Signal Ground – Secondary |
9 | – | Do not connect |
RS 485 Redundant Pin Assignment DA 26.30.5024.4…
1 | RS 485 A (1) | Interface 1 – Non-inverted Input/Output |
2 | RS 485 B (2) | Interface 1 – Inverted Input/Output |
# | RS 485 A (2) | Interface 2 – Non-inverted Input/Output |
4 | +V DC (2) | Supply Voltage – Secondary |
5 | Case GND | Case Ground |
6 | +V DC (1) | Supply Voltage – Primary |
7 | GND (1) | Supply Ground – Signal Ground – Primary |
8 | GND (2) | Supply Ground – Signal Ground – Secondary |
9 | RS 485 B (2) | Interface 2 – Inverted Input/Output |
RS 485 Interface (4-Wire) DA 26.30.5024.5…
1 | RS 485 A (Rx) | Receiver – Non-inverted – Input |
2 | RS 485 B (Rx) | Receiver – Inverted – Input |
3 | RS 485 A (Tx) | Transmitter – Non-inverted – Output |
4 | +V DC (2) | Supply Voltage – Secondary |
5 | Case GND | Case Ground |
6 | +V DC (1) | Supply Voltage – Primary |
7 | GND (1) | Supply Ground – Signal Ground – Primary |
8 | GND (2) | Supply Ground – Signal Ground – Secondary |
9 | RS 485 B (Tx) | Transmitter – Inverted – Output |