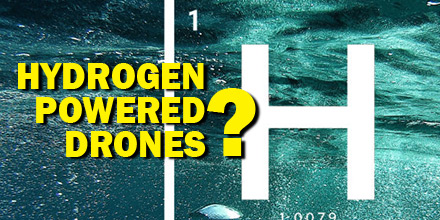
Battery life.
This continues to be one of the biggest challenges for drone operators.
Currently, the average flight time of most consumer drones is limited to around 20 minutes. Of course, this number varies depending on many things - weather conditions, payload, etc.
Ultimately, though, battery life continues to be a challenge for long flight operations. Eventually, a drone must return and recharge or switch out batteries before operations can continue.
Battery manufacturers, of course, continuously work to improve battery technology. But, there may be a completely new solution on the horizon...hydrogen fuel cells.
Recently, researchers in Sydney, Australia, successfully conducted UAV test flights using hydrogen-powered fuel cells. The results were promising.
Hydrogen: the future of drone power?
Hydrogen is one of the cleanest energies available on earth.
Though hydrogen fuel comes with some risks, the National Hydrogen Association argues that most are overblown. With careful use by qualified professionals, hydrogen may provide the answer to the challenge of a short battery life.
The research in Sydney seem to bear this out. Previously, the team tested hydrogen-only fuel cells and determined they were a viable energy source for drones.
The most recent tests used a triple hybrid propulsion system which included a combination of batteries, hydrogen fuel cells and a super capacitor.
The hybrid propulsion system helped researchers improve the robustness and flexibility of hydrogen fuel powered drones. Plus, the hydrogen fuel provided much greater range and endurance when compared to electric powered UAVs.
As such, if the technology develops it could have a revolutionary effect on the drone industry. Benefits include longer flight time, improved flight efficiency, and the development of more advanced UAVs.
The Wave of the Future?
If the finding by the scientists in Sydney and by other similar projects are anything to go by, it would seem that hydrogen powered drones are the wave of the future.
For one, the use of hydrogen enables drone operators to conduct their work for longer periods without interruptions. Plus, continued development of this technology would eventually result in decreased cost and greater implementation.
Advantages of using hydrogen fuel cells extend beyond improved efficiency and flight times, too.
Plus, vehicles powered by hydrogen fuel cells have faster take-off, enhanced climbing ability and more stable flying.
The fuel is more environmentally friendly. It produces no carbon dioxide emissions. In addition, hydrogen-powered drones tend to be much quieter than conventional electric powered ones.
Overall outlook
Currently, the price tag of this technology is a hindrance to many potential users. Driving down hydrogen fuel cell costs is one of the challenges of widespread adoption of this technology.
Researchers in Sydney believe the hybrid solution they implemented could be key to lowering costs. And hybrid technology, similar to hybrid cars which utilize a combination of fossil fuel and electric batteries, may be one way to gain widespread adoption.
With so many benefits, hydrogen-powered drones could indeed be the wave of the future.